Kleemann MOBIREX MR130I PRO
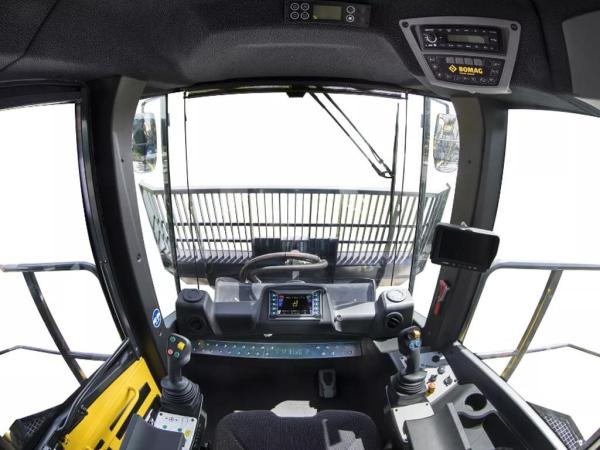
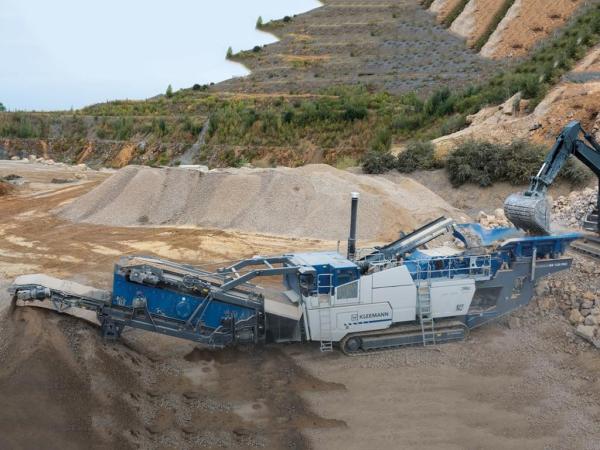
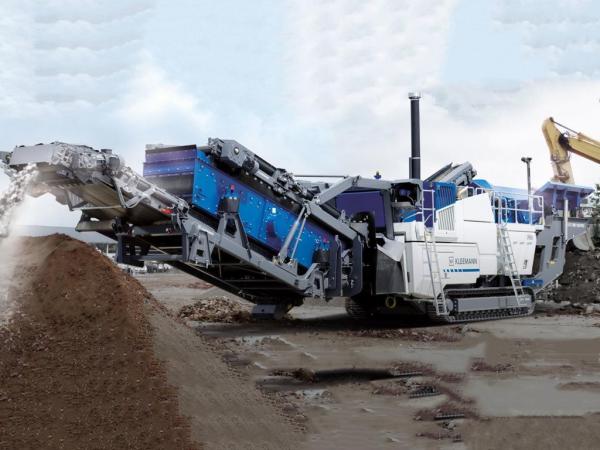
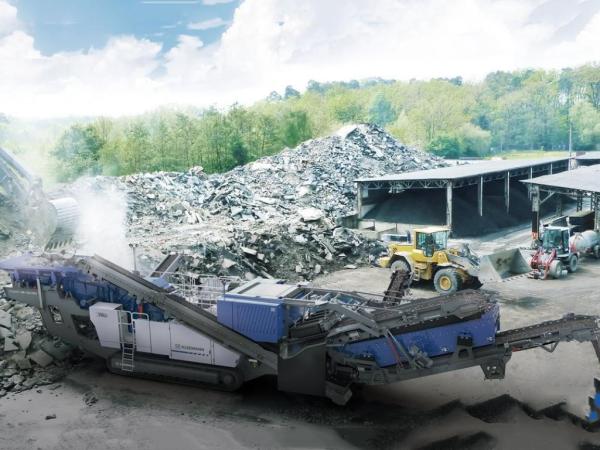
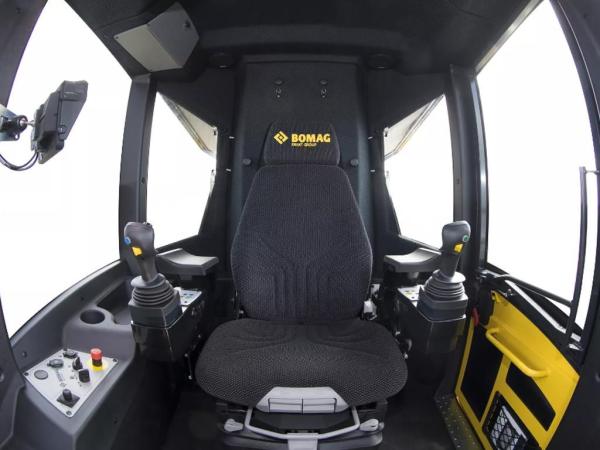
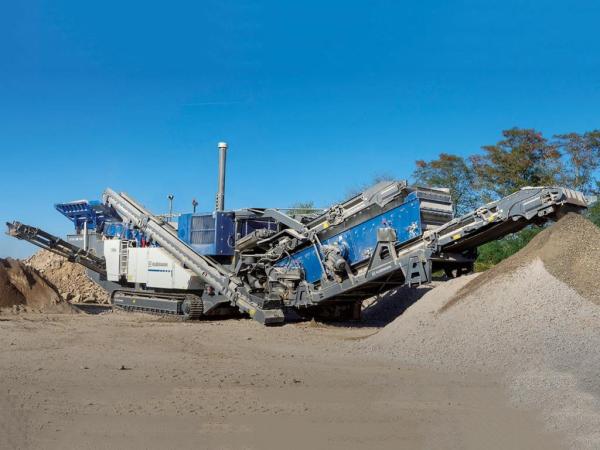
Make | Kleemann |
Model | MOBIREX MR130I PRO |
Type | Mobile Impact Crushers |
How can we help?
Description
MR 130I PRO — MOBILE IMPACT CRUSHER
MOBILE IMPACT CRUSHERS
The mobile impact crushers MOBIREX are used in soft to medium-hard natural rock and in recycling. The capacity of the plants is enormous - and the focus is not only on pure volume reduction. Cost and environmental awareness, availability, versatility and, above all, the quality of the final product are important aspects. With the MOBIREX plants stone is crushed so that the grain shape, grain size distribution, and cleanliness meet the high requirements of the standards for concrete and asphalt aggregates.
PROPERTIES
The MOBIREX MR 130(i) PRO covers a very wide application range in natural stone and recycling. A positive feature of the plant is its all-electric drive concept with the option of an external power supply. The CO2-free operation guarantees low energy consumption per ton of final product.
• Generously dimensioned double-deck prescreen with 2.9 m2 open screening surface
• Fully hydraulic gap adjustment and overload system
• E-DRIVE diesel-electric drive concept, external power supply (optional)
• Simple and intuitive SPECTIVE control concept
• Powerful double-deck post screening unit - use as single-deck and double-deck screen
CONTROL SYSTEM
INTUITIVE CONTROL CONCEPT SPECTIVE – FOR SIMPLE OPERATION
The easy-to-operate control concept SPECTIVE allows the machines to be operated at a touch panel. All components and functions can be controlled comfortably from the group.
SPECTIVE guides the operator step by step through the starting procedure. The start screen provides a graphical view of the plant with all adjustable functions at a glance. When the desired function is selected, clear instructions guide users through all operating steps. If a fault occurs, a fault diagnosis appears on the display. Fault localization, the description and remedy tips result in reduced downtimes. The 12” touch panel is resistant to dust and always easy to read thanks to the light intensity and high contrast. It reacts to fingers, pen, or gloves.
MATERIAL FLOW
CONTINUOUS FEED SYSTEM (CFS) - For a continuous crusher feed.
Uniform loading is indispensable for a good product, optimum throughput and low wear.
To ensure that the crushing chamber is always evenly filled, the Continuous Feed System (CFS) monitors the crusher level (jaw crusher and cone crusher) or the load at the rocker and rotor as well as the motor utilization (impact crusher).
Independently of this, the CFS regulates the frequency of the vibrating feeder and prescreen. A backlog on the prescreen is thus avoided and crusher utilization is optimized. When the crushing chamber is free again after overloading, material transport is continued without a delay.
The CFS facilitates the work of the operator because the machine automatically guarantees a homogeneous material flow, thus ensuring optimum loading of the crusher.
INNOVATIVE DIESEL-ELECTRIC DRIVE CONCEPT – IMPRESSIVE PERFORMANCE WITH THE BEST POSSIBLE CONSUMPTION VALUES
The crushing plants are equipped with efficient, powerful diesel-electric drives. They ensure environmentally friendly operation combined with low fuel consumption.
Efficient and powerful diesel-electric drive (A) for low fuel consumption (crusher and all conveyor belts are driven electrically)
External power supply (B) for even more cost-effective use in quarries.
SPECTIVE CONNECT
Operator information App, unidirectional communication
All relevant data at a glance
• Dashboard
• Cameral live image
• Reporting
• Messages and troubleshooting aids
• Overview of all plants in the train
The operator can remain in the excavator/wheel loader
• No interruption to the work process
• Increase in work safety
STANDARD EQUIPMENT
• Hydraulically-folding feed hopper, can be operated from ground
• Frequency-controlled vibrating feeder
• Frequency-controlled prescreen, stepless speed control
• Continuous Feed System (CFS) for optimum crusher loading
• Automatic crusher gap adjustment
• Integrated overload protection
• Rotor lock & turn device: system for securely turning and locking the rotor for maintenance tasks or clearing blockages
• Swivel arm for changing rotor ledges
• SPECTIVE control concept: menu-guided user interface, 12-inch control panel; telematics system for efficient fleet and service management
• SPECTIVE remote control: wired and radio remote control incl. switch-off function for feeding unit
• LED lighting
• Water spray system for dust reduction
OPTIONS
• Hopper extension: hydraulically folding
• Hopper filling aids for rearward loading: width of feed opening 3,300 mm
• Side discharge conveyor, rigid: can be fitted on the left and right, must be disassembled for transport
• Foldable side discharge conveyor, hydraulically foldable, configurable on both sides, remains on machine for transport
• Co-vibrating crusher bypass flap for flexible change-over between side discharge and crusher bypass
• External power supply for efficient mains operation
• Reversible fan for dedusting the engine compartment Raised engine air intake for reduced dust load
• Power pack housing for damping noise sources, incl. sealing of the power pack base as noise and dust protection
• Climate control packages: hot climate or cold climate package
• Electromagnetic separator or permanent magnetic separator, suspended flexibly by chains, can be raised and lowered hydraulically
• Reinforced conveyor belt for crusher discharge conveyor
• Double-deck post screening unit, use as a single-deck or double deck screen, production of up to two classified final grain sizes, incl. swiveling return conveyor
• Return conveyor frequency converter for precise speed control
• Middle grain conveyor, remains on the post screening unit for transport
• Belt scale, available for crusher discharge conveyor, side discharge conveyor, middle grain conveyor and fine grain conveyor
• Belt cover canvas, for rigid side discharge conveyor, crusher discharge conveyor and fine grain conveyor
• Wind sifter for cleaning the oversize grain and medium grain to remove foreign and lightweight materials
• SPECTIVE CONNECT for displaying all important machine information directly on the smartphone
• mall radio remote control with key operating functions > Quick Track for selecting machine operating mode quickly and easily, operation via radio remote control
• Line coupling for interlinking with other KLEEMANN plants
• Premium lighting
• Camera system for monitoring the feeding unit and the transfer point to the return conveyor from the ground, also available with radio extension, additional connection to SPECTIVE CONNECT
Similar models may be shown in addition to the featured model. Equipment may be shown with options.
Specifications are subject to change without prior notice.
Specifications
- Crusher - Adjustment of impact toggles: infinitely variable, fully hydraulic
- Crusher - Crusher drive type, approx. (kW): electric, 250
- Crusher - Crusher inlet width x height: 1,300 x 900
- Crusher - Crusher weight approx. (lbs): 17,500
- Crusher - Details: 1) Depending on type and composition of feed material, feed size, prescreening as well as target final grain size 2) With final grain size 0“ – 1.8“ with approx. 10 – 15 % oversize grain 3) With final grain size 0“ – 1.3“ with approx. 10 – 15 % oversize grain 4) All electric ancillary drives
- Crusher - Impact crusher type: SHB 130 - 090
- Crusher - Rotor diameter: 1,200 mm
- Crusher Discharge Conveyor - Discharge height approx. :
- Crusher Discharge Conveyor - Width x length: 1,435 x 2,670
- Discharge Chute - Width x length: 56" x 8' 10"
- Feeding Unit - Details: 1) Depending on type and composition of feed material, feed size, prescreening as well as target final grain size 2) With final grain size 0“ – 1.8“ with approx. 10 – 15 % oversize grain 3) With final grain size 0“ – 1.3“ with approx. 10 – 15 % oversize grain 4) All electric ancillary drives
- Feeding Unit - Feed height (with extension): 4,350 (4,840)
- Feeding Unit - Hopper volume (with extension) (yd³): 5 (9)
- Feeding Unit - Max. feed size: 1,040 x 650
- Feeding Unit - Width x length (with extension): 2,250 x 3,700 (3,000 x 3,700)
- Performance Levels - Details: 1) Depending on type and composition of feed material, feed size, prescreening as well as target final grain size 2) With final grain size 0“ – 1.8“ with approx. 10 – 15 % oversize grain 3) With final grain size 0“ – 1.3“ with approx. 10 – 15 % oversize grain 4) All electric ancillary drives
- Performance Levels - Feed capacity up to approx. (t/h): 600
- Performance Levels - Production output with demolished concrete up to approx. (t/h): 400 (1)
- Performance Levels - Production output with limestone up to approx. (t/h): 400 (1)
- Performance Levels - Production output with milled asphalt up to approx. (t/h): 220 (2)
- Performance Levels - Production output with rubble up to approx. (t/h): 450 (1)
- Post Screening Unit (Optional) - Discharge height, fine grain conveyor approx. (mm): 4,000
- Post Screening Unit (Optional) - Return conveyor: Width x length approx. (mm) : 650 x 11,200
- Post Screening Unit (Optional) - Side discharge conveyor, medium grain: Discharge height approx. (mm): 3,400
- Post Screening Unit (Optional) - Side discharge conveyor, medium grain: Width x length approx. (mm) : 650 x 6,800
- Post Screening Unit (Optional) - Type: Double-deck screen
- Post Screening Unit (Optional) - Width x length of lower deck approx. (mm) : 1,550 x 4,700
- Post Screening Unit (Optional) - Width x length of upper deck approx. (mm) : 1,550 x 5,500
- Power Supply Unit - Drive concept: diesel-electric
- Power Supply Unit - Drive output of Scania diesel engine (kW): 478
- Power Supply Unit - Generator (kVA): 550
- Prescreening - Type: Double-deck heavy-piece screen
- Prescreening - Width x Length (inch) : 1,210 x 2,400
- Side Discharge Conveyor Can Be Folded Hydraulically (Optional) - Discharge height approx. (mm): 3,400
- Side Discharge Conveyor Can Be Folded Hydraulically (Optional) - Width x Length (mm): 650 x 6,000
- Side Discharge Conveyor Rigid (Optional) - Discharge height approx. (extended): 3,550
- Side Discharge Conveyor Rigid (Optional) - Width x length (extended): 650 x 6,600
- Transport - Details: 1) Depending on type and composition of feed material, feed size, prescreening as well as target final grain size 2) With final grain size 0“ – 1.8“ with approx. 10 – 15 % oversize grain 3) With final grain size 0“ – 1.3“ with approx. 10 – 15 % oversize grain 4) All electric ancillary drives
- Transport - Max. transport width: 3,455
- Transport - Transport dimensions with post screening unit:
- Transport - Transport dimensions without options:
- Transport - Transport height: 3,900
- Transport - Transport length approx. : 20,965
- Transport - Transport length with screening unit approx. (mm) : 23,275
- Transport - Transport weight max. configuration approx. (kg): 83,500
- Transport - Transport weight of basic plant approx. (kg): 64,000
- Transport - Transport weight of screening unit approx. (kg): 13,000 (3)
- Transport - Transport width with post screening unit approx. (mm) : 3,500
- Vibrating Feeder - :
- Vibrating Feeder - Width x length: 1,100 x 2,700