Vogele AB 340
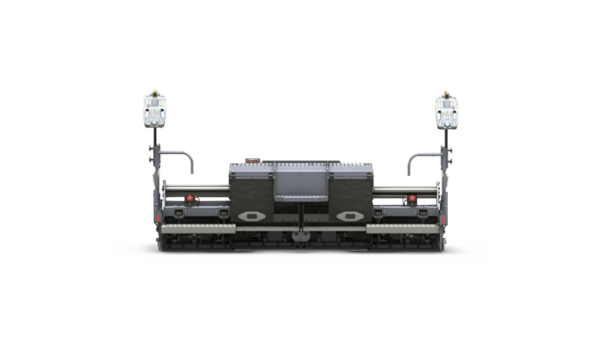
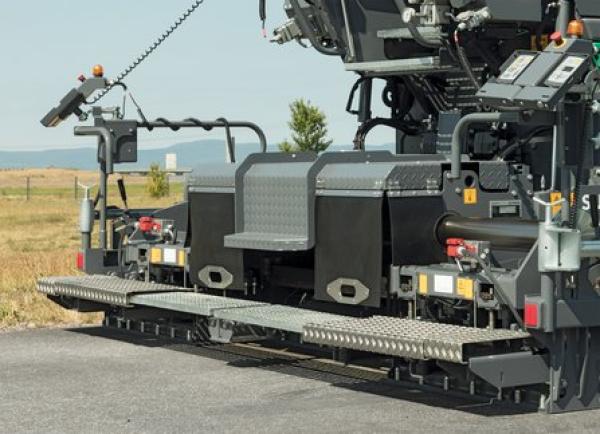
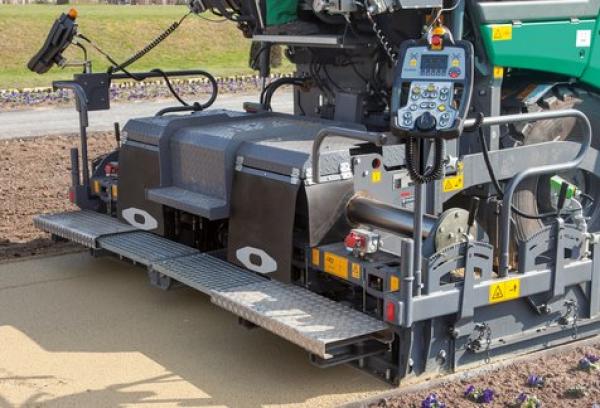
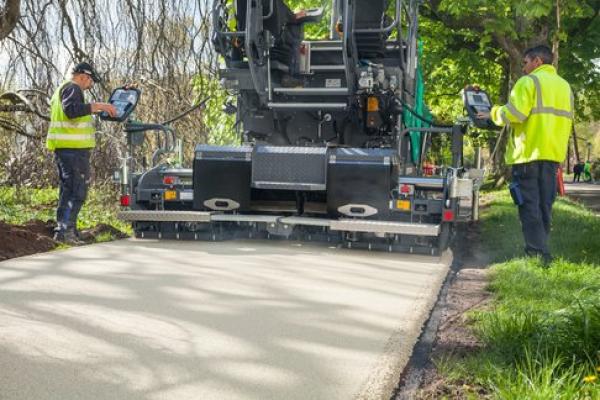

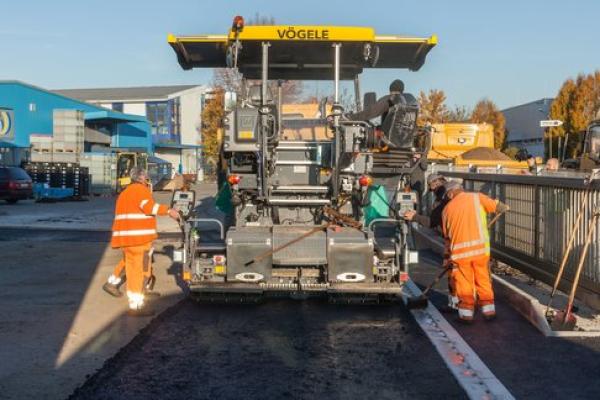
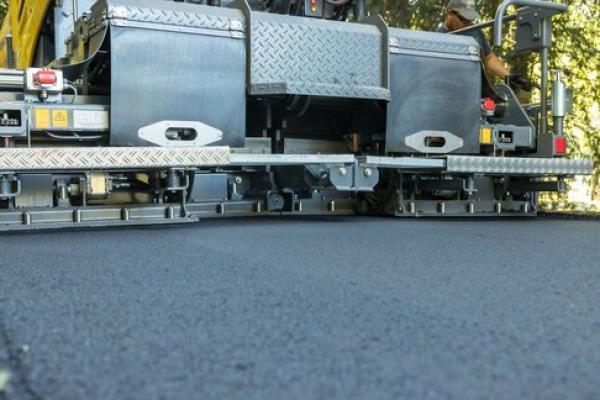
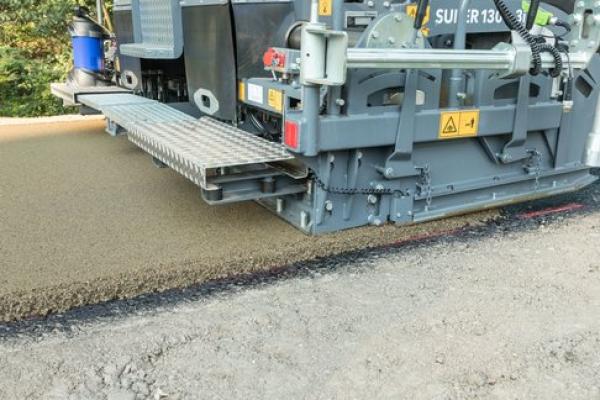
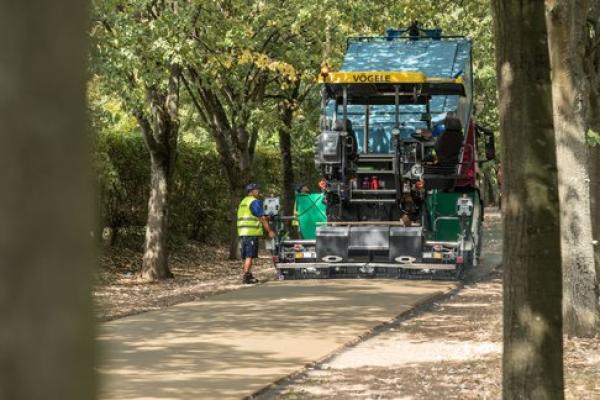
Make | Vogele |
Model | AB 340 |
Type | Extending Screeds |
How can we help?
Description
The perfect Compact Class screed
The AB 340 Extending Screed is the ideal screed for compact pavers of the 1000 and 1300 class. With a basic width of 5 ft 11 in and a maximum paving width of 16 ft 5 in, the screed is ideal for building combined foot and cycle paths, minor rural roads and narrow roads or squares.
Models
Telescoping system
The operating principle of all VÖGELE extending screeds is the single-tube telescoping system. Even at maximum extension, half of the three-part, generously-sized telescoping tube is clamped, ensuring optimum stabilization. As the telescoping system is arranged at a high level, this prevents any contact with paving mix.
Heating System
VÖGELE has put its faith in electric screed heating for decades. This extensive experience, in combination with continuous further development, means that VÖGELE screeds are now brought to temperature quickly and evenly.
Compaction technology
VÖGELE sets the benchmark with products that deliver a phenomenal degree of precompaction in the paving process. Cutting-edge technology and the most advanced materials guarantee the outstanding performance and reliability of VÖGELE compaction technology. This applies to all VÖGELE compacting systems, from vibrators all the way to the VÖGELE high-compaction system with tamper and pressure bars.
Manufacturing Technology
VÖGELE screeds feature leading-edge technology made possible by state-of-the-art production processes. The first of these processes, the precision cutting to shape of extremely wear-resistant sheet steel, takes place on laser cutting stations. Robots which operate continuously to a consistently high standard ensure long-lasting, stable welds.
Specifications
- COMPACTING SYSTEMS - Compacting systems: V, TV
- COMPACTING SYSTEMS - Frequency (max.): 50 Hz
- COMPACTING SYSTEMS - Speed (max.): 1,700 rpm
- COMPACTING SYSTEMS - Stroke (TV): 0.16 in
- COMPACTING SYSTEMS - Vibrators (V): eccentric vibrators
- DIMENSIONS AND WEIGHTS - Depth (in transport position): Screed Depth AB 340 3 ft 7 in
- DIMENSIONS AND WEIGHTS - Weight of basic screed: Screed Weight AB 340 V 2,980 lbs AB 340 TV 3,420 lbs
- PAVING WIDTHS - Basic width: 5 ft 11 in
- PAVING WIDTHS - Cut-off shoes: 2 x 1 ft 9 in
- PAVING WIDTHS - Hydraulically adjustable: 5 ft 11 in to 11 ft 2 in
- PAVING WIDTHS - Length: Extra bolt-on extensions Bolt-on extensions (V, TV) 10 in (V, TV) 16 in (TV) 22 in (TV) 32 in
- PAVING WIDTHS - Maximum paving width: 16 ft 5 in
- PAVING WIDTHS - Minimum paving width: 2 ft 6 in
- PROFILE SETTINGS - Crown adjustment: -2.5 % to 3 %
- PROFILE SETTINGS - Height adjustment, extending units: -1 in to 1 in
- PROFILE SETTINGS - Slope, extending units (max.): 2 %
- PROFILE SETTINGS - Version: mechanical, hydraulic as an option
- SCREED HEATING - Heating rods: on screed plates and in tamper bars
- SCREED HEATING - Output generation: three-phase AC generator
Links
Copy Set
Telescoping system
The operating principle of all VÖGELE extending screeds is the single-tube telescoping system. Even at maximum extension, half of the three-part, generously-sized telescoping tube is clamped, ensuring optimum stabilization. As the telescoping system is arranged at a high level, this prevents any contact with paving mix.
Heating System
VÖGELE has put its faith in electric screed heating for decades. This extensive experience, in combination with continuous further development, means that VÖGELE screeds are now brought to temperature quickly and evenly.
Compaction technology
VÖGELE sets the benchmark with products that deliver a phenomenal degree of precompaction in the paving process. Cutting-edge technology and the most advanced materials guarantee the outstanding performance and reliability of VÖGELE compaction technology. This applies to all VÖGELE compacting systems, from vibrators all the way to the VÖGELE high-compaction system with tamper and pressure bars.
Manufacturing Technology
VÖGELE screeds feature leading-edge technology made possible by state-of-the-art production processes. The first of these processes, the precision cutting to shape of extremely wear-resistant sheet steel, takes place on laser cutting stations. Robots which operate continuously to a consistently high standard ensure long-lasting, stable welds.