Wirtgen W 50 Ri
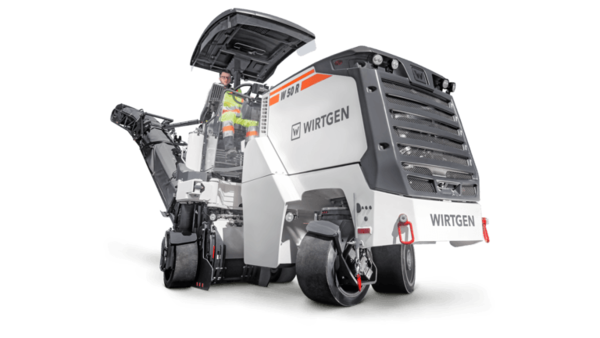
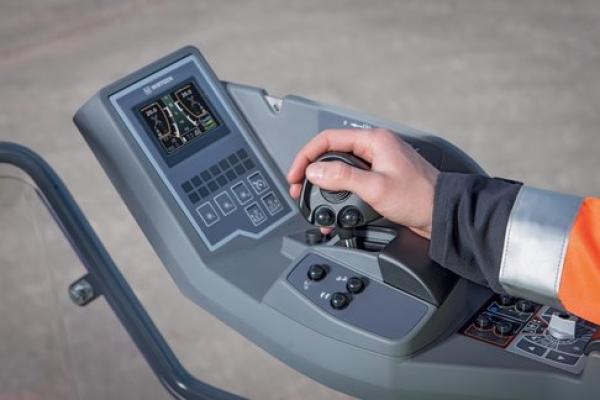
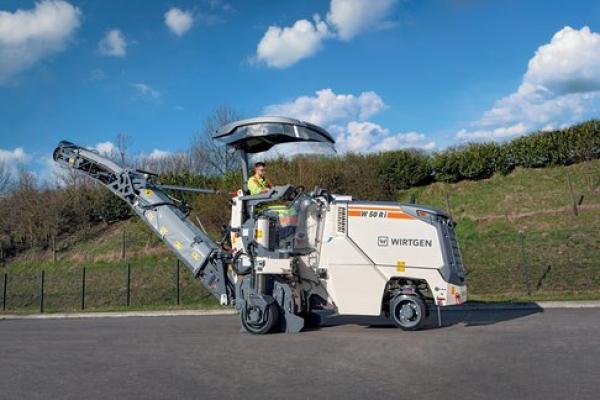
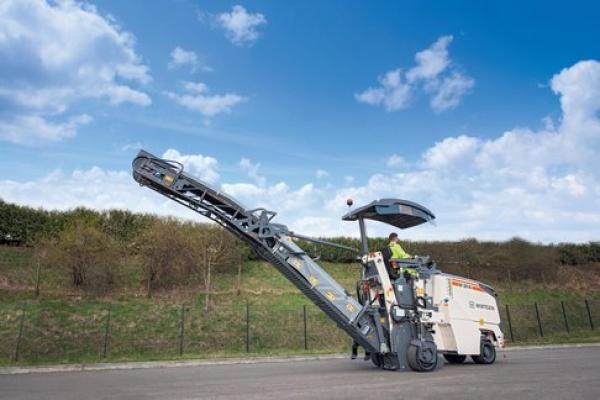
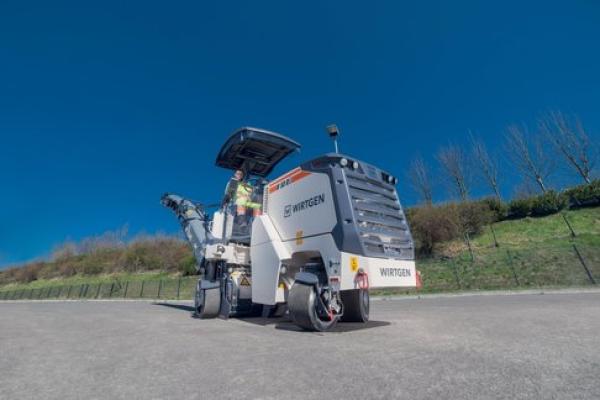
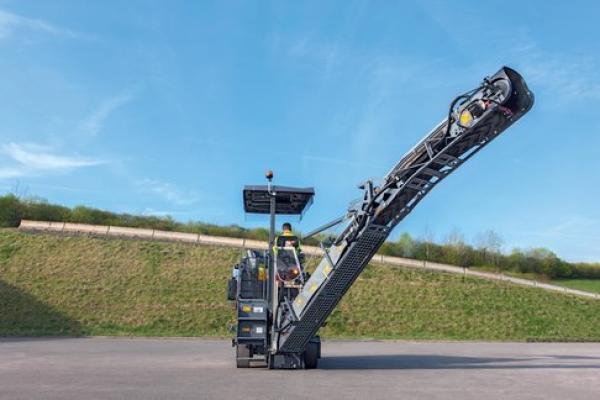
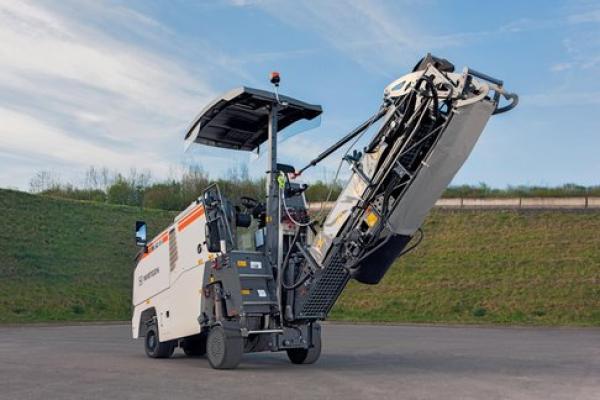
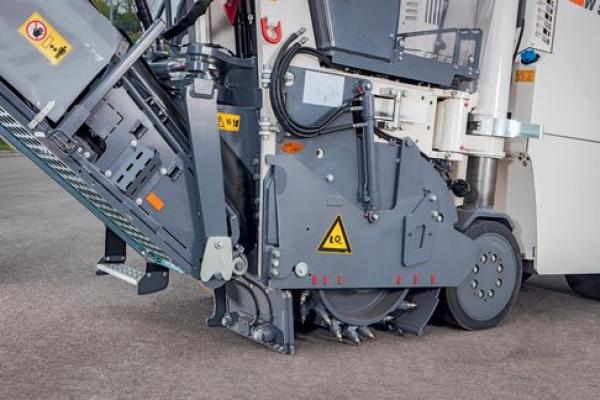
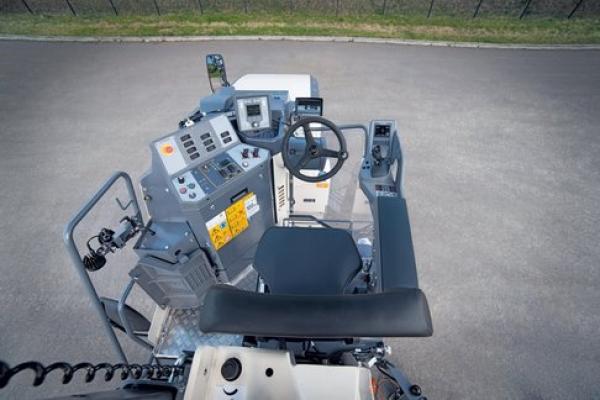
Make | Wirtgen |
Model | W 50 Ri |
Type | Small Milling Machines |
How can we help?
Description
Powerful rear-loading machine for professional milling operations
-
The powerful half-meter cold milling machine convinces with its efficient operating concept.
-
The easy-to-use additional and automatic functions increase its performance potential for carrying out construction jobs at a fast pace.
-
The levelling system LEVEL PRO PLUS integrated in the machine control system provides precise milling results.
-
A variety of various milling drums enable high levels of flexibility and machine performance.
-
To optimize the material loading process, the powerful rear-loading system can be flexibly adjusted.
Models
Control technology
All WIRTGEN machines feature a built-in, high-quality machine control system. The fact that the majority of its software is developed in-house plays a key role in this regard – WIRTGEN has placed a special focus on ongoing development, thus significantly increasing the operational reliability of its machines. Many years of experience in software and hardware development also makes it possible to achieve more flexible and sophisticated machine functionality in terms of the range of applications and individual customer requirements.
WIRTGEN leveling technology
WIRTGEN’s leveling technology adjusts height, depth, and pitch for extremely accurate results. In the process, the system permanently compares the actual values to predefined target values and adjusts the deviations proportionally. This state-of-the-art machine technology consistently guarantees outstanding leveling results and significantly reduces the machine operator’s workload.
WIRTGEN offers customers reliable hardware and software developed in-house. In this context, a variety of systems are used depending on the construction project and local conditions at the job site.
Cold milling with small milling machines
Small milling machines are equipped with a wheeled chassis and a milling drum positioned at the rear of the machine. The granulated RAP separated by the rotating milling drum is collected by a slewing discharge belt located at the rear of the machine and immediately conveyed to waiting trucks. That is why small milling machines are also called rear loaders. The compact rear loaders are designed to be operated by a single person. In addition, they are usually extremely maneuverable and have a retractable right rear wheel.
WIRTGEN cutting technology
High quality results are the goal of every construction project. This applies to road rehabilitation using cold milling machines and cold recyclers as well as to soil stabilization and the extraction of minerals with surface miners. In order to remove pavement with precision and efficiency, it is essential that the drum, pick holder, and pick work together perfectly.
WIRTGEN is the market leader in cutting technology and offers customers high-performance cutting systems whose components are designed to be fully compatible. In addition, WIRTGEN continuously makes advancements to these cutting technology components, incorporating its practical experience and feedback from customers into the process.
Specifications
- SPECIFICATIONS - Displacement: 1.1 Imp.gal
- SPECIFICATIONS - Exhaust emissions category: US EPA Tier 4f
- SPECIFICATIONS - Max. milling speed: 1.8 mph
- SPECIFICATIONS - Max. travel speed 3-wheeled model: 5 mph
- SPECIFICATIONS - Maximum power: 105 kW / 141 hp
- SPECIFICATIONS - Milling depth max.: 8 in
- SPECIFICATIONS - Milling width: 20 in
- SPECIFICATIONS - Operating weight, CE: 15,278 lbs
- SPECIFICATIONS - Travel speed in milling gear in 4-wheel drive design: 7.5 mph
Links
Copy Set
Control technology
All WIRTGEN machines feature a built-in, high-quality machine control system. The fact that the majority of its software is developed in-house plays a key role in this regard – WIRTGEN has placed a special focus on ongoing development, thus significantly increasing the operational reliability of its machines. Many years of experience in software and hardware development also makes it possible to achieve more flexible and sophisticated machine functionality in terms of the range of applications and individual customer requirements.
WIRTGEN leveling technology
WIRTGEN’s leveling technology adjusts height, depth, and pitch for extremely accurate results. In the process, the system permanently compares the actual values to predefined target values and adjusts the deviations proportionally. This state-of-the-art machine technology consistently guarantees outstanding leveling results and significantly reduces the machine operator’s workload.
WIRTGEN offers customers reliable hardware and software developed in-house. In this context, a variety of systems are used depending on the construction project and local conditions at the job site.
Cold milling with small milling machines
Small milling machines are equipped with a wheeled chassis and a milling drum positioned at the rear of the machine. The granulated RAP separated by the rotating milling drum is collected by a slewing discharge belt located at the rear of the machine and immediately conveyed to waiting trucks. That is why small milling machines are also called rear loaders. The compact rear loaders are designed to be operated by a single person. In addition, they are usually extremely maneuverable and have a retractable right rear wheel.
WIRTGEN cutting technology
High quality results are the goal of every construction project. This applies to road rehabilitation using cold milling machines and cold recyclers as well as to soil stabilization and the extraction of minerals with surface miners. In order to remove pavement with precision and efficiency, it is essential that the drum, pick holder, and pick work together perfectly.
WIRTGEN is the market leader in cutting technology and offers customers high-performance cutting systems whose components are designed to be fully compatible. In addition, WIRTGEN continuously makes advancements to these cutting technology components, incorporating its practical experience and feedback from customers into the process.